About Aluminum Casting Chronicles: Strategies, Trends, and Tips
About Aluminum Casting Chronicles: Strategies, Trends, and Tips
Blog Article
Check Out the Globe of Aluminum Spreading: Insider Methods and tricks
In the realm of production, light weight aluminum spreading stands as an essential process, essential for the production of a broad selection of products. Behind the relatively simple strategy exist a plethora of complex elements, typically unbeknownst to many. As we browse via the globe of light weight aluminum casting, there exists a world of expert tricks and methods that can raise the top quality of the last items and enhance the manufacturing process. By revealing these hidden gems and checking out the subtleties of this craft, a whole brand-new measurement of possibilities emerges, assuring to change the method we perceive and engage with aluminum spreading.
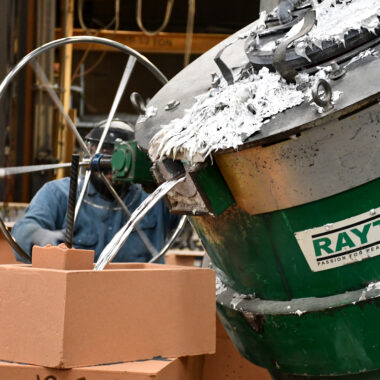
The Basics of Aluminum Spreading
Aluminum spreading, a fundamental process in production, includes the pouring of liquified aluminum into a mold to achieve preferred structures and forms. This flexible strategy is widely utilized across different industries as a result of aluminum's outstanding properties such as high strength-to-weight proportion, corrosion resistance, and thermal conductivity.
The procedure begins with the melting of aluminum in a heating system at temperature levels exceeding 1220 ° F(660 ° C ) When the aluminum reaches its liquid state, it is poured right into a pre-designed mold cavity. The mold, commonly made from materials like steel or sand, figures out the last form of the actors aluminum part.
After putting, the aluminum is entrusted to cool and strengthen within the mold and mildew - about aluminum casting. This cooling period is essential as it establishes the integrity and quality of the final item. Once solidified, the mold and mildew is gotten rid of, revealing the recently formed light weight aluminum casting
Expert Tips for Successful Casting
To attain optimum outcomes in light weight aluminum spreading, careful interest to information during the mold and mildew layout phase is essential for ensuring effective results. One insider suggestion for effective spreading is to very carefully think about eviction system. The layout of eviction system plays an important duty in managing the flow of molten aluminum into the mold cavity, making sure correct filling and reducing defects like air entrapment. Furthermore, keeping the appropriate metal temperature level is crucial for attaining top quality castings. Surveillance and controlling the metal temperature throughout the spreading procedure can help prevent issues such as premature solidification or porosity in the final item.
A well-prepared mold and mildew surface area can add to much better metal flow, decreased turbulence, and boosted surface coating on the actors part. By paying close attention to these expert tips, suppliers can improve the high quality and efficiency of their aluminum casting processes.
Advanced Strategies in Light Weight Aluminum Spreading
Using advanced methods and cutting-edge techniques, the world of light weight aluminum casting has seen a significant evolution in the direction of advanced techniques that push the limits of conventional techniques. One such technique is vacuum cleaner casting, which includes creating a vacuum cleaner atmosphere to remove air from the mold dental caries, bring about better and more intricate castings with decreased porosity. Furthermore, investment casting, also called lost-wax spreading, is a polished approach that enables for intricate forms and slim wall surfaces, resulting in exact and detailed aluminum parts.
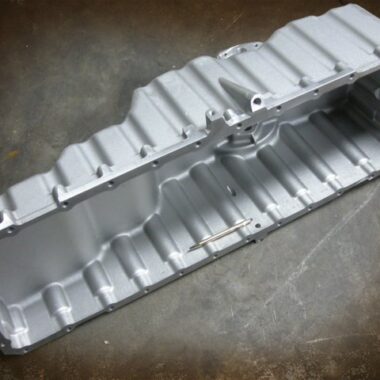
Furthermore, progressed simulation software plays a critical role in optimizing spreading layouts and predicting possible flaws, allowing for pop over to these guys changes to be made before the real casting process starts. By embracing these advanced methods, makers can raise their aluminum casting abilities to brand-new heights, meeting the demands of contemporary industries with precision and advancement.
Understanding Various Casting Techniques
In the realm of manufacturing, a thorough understanding of different casting approaches is essential for achieving optimum results in steel fabrication procedures. Different spreading techniques provide one-of-a-kind advantages and are chosen based on variables such as the complexity of the style, manufacturing quantity, product demands, and price factors to consider. One of one of the most common spreading methods is sand casting, where a mold is produced utilizing sand as the primary material. Sand spreading is versatile, cost-effective, and appropriate for generating large components.
One more popular spreading approach is pass away casting, which includes infusing molten metal right into a mold dental caries under high stress. Die casting is understood for its high precision, smooth surface coating, and the capacity to produce complicated forms with tight tolerances. Gravity casting, on the various other hand, counts on gravity to fill up the mold cavity with molten metal. This approach appropriates for creating simpler shapes and is cost-effective for small to tool production runs. By comprehending the subtleties of various spreading approaches, producers can make enlightened decisions to optimize their manufacturing processes and attain the desired end results.
Maximizing Effectiveness in Casting Workflow
With a firm understanding of the subtleties of different casting approaches, producers can simplify their procedures to improve effectiveness in steel fabrication processes. Making the most of effectiveness in casting procedures needs a methodical technique that focuses on enhancing every action of the spreading procedure.
Moreover, spending in innovative modern technology and tools can significantly enhance efficiency in casting procedures. Automated systems, robotics, and computer-aided layout (CAD) software program can improve processes, reduce mistakes, and increase result. Additionally, training employees on the most up to date methods and finest methods can likewise add to taking full advantage of performance in casting procedures.
Regular maintenance of equipment and devices is crucial to minimize and protect against break downs downtime - about aluminum casting. Carrying out a proactive upkeep routine can aid identify prospective issues prior to they intensify, guaranteeing smooth operations and nonstop manufacturing. In general, by prioritizing efficiency and continual enhancement, manufacturers can enhance visit their casting operations and stay affordable in the industry
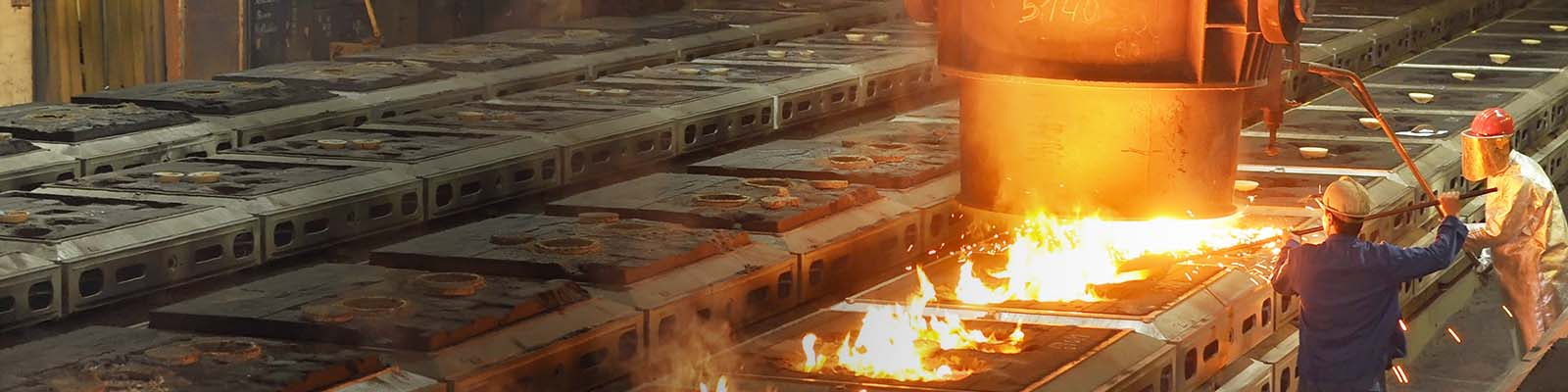
Conclusion
Finally, the globe of light weight aluminum casting provides a vast array of possibilities for those aiming to develop durable and intricate steel things. By mastering the fundamentals, utilizing expert pointers, and exploring sophisticated techniques, individuals can attain terrific success in their casting endeavors. Understanding the various spreading methods and optimizing effectiveness in procedures are vital elements to accomplishing top notch cause light weight aluminum casting. With devotion and method, one can really unlock the possibility of this flexible metalworking process.
One such strategy is vacuum spreading, which includes developing a vacuum atmosphere to get rid my company of air from the mold tooth cavity, leading to higher quality and even more intricate spreadings with minimized porosity (about aluminum casting). Furthermore, investment spreading, also understood as lost-wax spreading, is a refined approach that enables for complicated forms and thin walls, resulting in accurate and thorough light weight aluminum parts
One of the most common casting techniques is sand spreading, where a mold and mildew is created making use of sand as the key product.Another prominent casting method is die casting, which involves injecting molten steel into a mold and mildew tooth cavity under high pressure. Understanding the various spreading techniques and optimizing performance in procedures are essential parts to attaining top quality outcomes in light weight aluminum casting.
Report this page